What is the Air Compressor Operating Cost?
How to calculate the air compressor cost for operating? The operating cost of an air compressor is the total cash you spend to run and care for the unit over time. It’s not only about flipping the switch and letting it hum- leaving costs sneak in from power use, parts wear, and routine service.
Here’s a quick look at what adds to your running costs:
- Power or fuel, the machine burns
- Regular checks and upkeep
- Belts, filters, oil, and other spares
- Dryers, separators, and other air gear
- Lost hours when things sit idle
Too many buyers zero in on sticker prices and stop there. The truth is the real outlay only begins at the checkout. Once you add energy, upkeep, parts, and downtime, the total ownership cost hits hard. Power use can chew up roughly 75 percent of the whole bill. That’s why seeing the full cost picture is key, especially in plants that run around the clock. Whether you’ve got a rotary screw or a piston compressor, knowing the numbers lets you trim waste, boost output, and protect your profit for years.
Cost of Compressed Air per CFM (Cubic Feet per Minute)
- How to calculate the air compressor cost for operating? The cost-per-CFM number tells you how razor-sharp or dull the wallet impact of your compressor is. To nail it down, take every cent spent in a year on electricity, upkeep, and any hidden extras, then divide it by the total air volume produced in CFM hours.
- That single figure lets you stack up every compressor layout side-by-side or eyeball the hard cash saved after an upgrade. You can slice the same data another way with the power cost per CFM, which pairs energy use straight to output volume.
Total Cost of Ownership (TCO) for an Air Compressor
Even though this post zeroes in on running expenses, keep in mind that operating costs usually soak up the biggest chunk of TCO. The full TCO picture also covers:
- Initial Purchase Price: What you pay upfront for the compressor plus extras like dryers, filters, and air receivers.
- Installation Costs: Money spent on labor, piping, wiring, and any other hook-up work.
- Operating Costs: Day-to-day power bills, maintenance parts, consumables, and the time your staff devotes to routine checks.
- Maintenance & Repair Costs: Routine checks, surprise fixes, spare parts, plus oil and grease.
- Disposal Costs: Not often thought about, yet crucial when the unit finally quits.
Across a decade, these day-to-day costs usually swallow 70-80% of total ownership, far exceeding what you paid at the start. That is why guessing compressor running costs is so important.
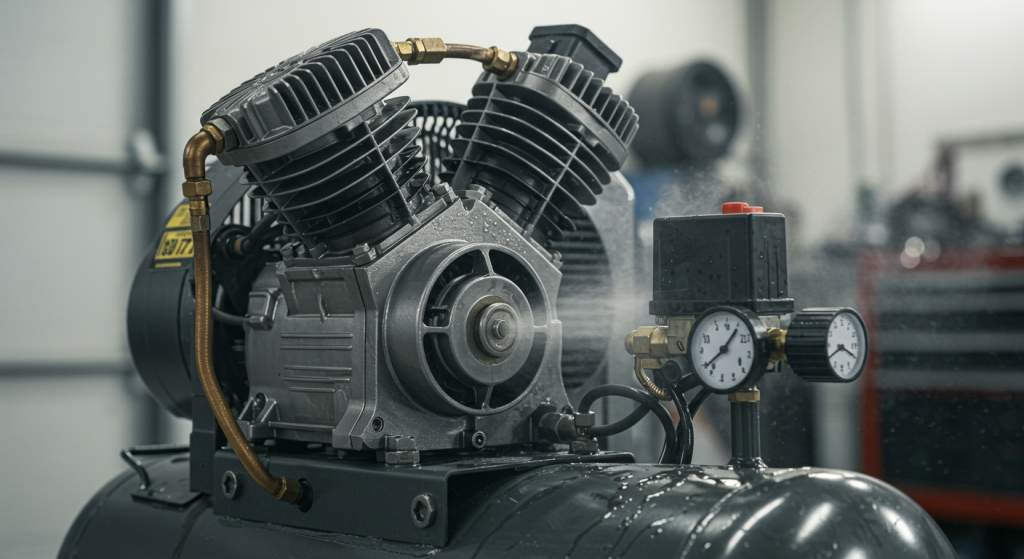
Factors That Affect Air Compressor Operating Cost
Here are the main items that add to your monthly bill.
1. Electricity Rate & Usage Hours
When power is pricey and machines run long, charges pile up.
- Big plants may also pay demand fees for peak draw.
- Running off-peak, when rates drop, can shave dollars off each bill.
2. Load/Unload Cycles
Fixed-speed machines spin at full blast even when no air is called for.
- That means power is burning while nothing useful happens.
- A Variable Speed Drive (VSD) unit ramps up and down with demand, saving as much as 35%.
3. Air Leaks
A small 1/8 hole at 100 PSI can drain more than $1,200 on power each year. Finding and fixing leaks must be part of regular upkeep.
4. Ambient Temperature
- Hot rooms force the compressor to work harder and cool more.
- Good ventilation and climate control keep costs lower.
Running an air compressor takes more than pushing a button- it means keeping an eye on maintenance every single week. If you skip the basics, motors can grind to a halt, parts can snap, and repair bills soar. Quickly, your once-reliable compressor starts acting old before its time.
The Main Upkeep Costs That Quietly Pile Up:
- Oil cost – In oil-lubed models, fresh, clean oil keeps bearings smooth, so swap it on schedule.
- Air dryer cost – Dryers zap humidity, but also electricity. Clean coils and drain traps to keep them lean.
- Air filter cost – Grimy filters choke airflow, forcing motors to pull extra amps. Replace them often to save energy.
- Service cost – Tighten belts, check hoses, and swap broken parts. A quick tune-up beats an all-day repair.
Reducing Compressed Air Costs: Proven Tips
- Choose the Right Size
Larger compressors pump extra air and bill you extra money. Consult sizing charts and match the unit to your daily demand.
- Optimize Pressure
Every 2 PSI above what you need adds about 1% to the power cost. Trim the pressure without hurting tools or tasks.
- Use VSD Compressors
Variable-speed drives slow the motor when demand dips, cutting power nearly in half at low loads.
- Schedule Preventive Maintenance
Replace clogged filters, top off oil, and check belts. Simple upkeep keeps machines happy and stops surprises.
- Conduct an Energy Audit
A quick review spots leaks, over-pressurization, and hidden waste so you can tackle issues fast.
Conclusion
Figuring what how to calculate the air compressor cost for operating goes far beyond a quick spreadsheet. Electricity, leaks, upkeep, and downtime all share the same wallet. Even small shops can unlock big savings and smooth cash flow by measuring each piece and tweaking the system. Simple tools like the air-compressor power-use formula, a cost-per-CFM calculator, and a total cost-of-ownership check let you spend smarter. At VIBRANT, we guide you in picking the right machine and in seeing clearly what it costs to run.